Drive efficiency
During 2017, Essity achieved SEK 1,231m in additional cost savings. The cost savings resulted from Essity’s focus on continuous improvements across the entire value chain. By maximizing production, continuously finding ways of reducing material, energy and logistics costs and minimizing waste, we reduce our costs and improve our earnings at the same time as we reduce the environmental impact.
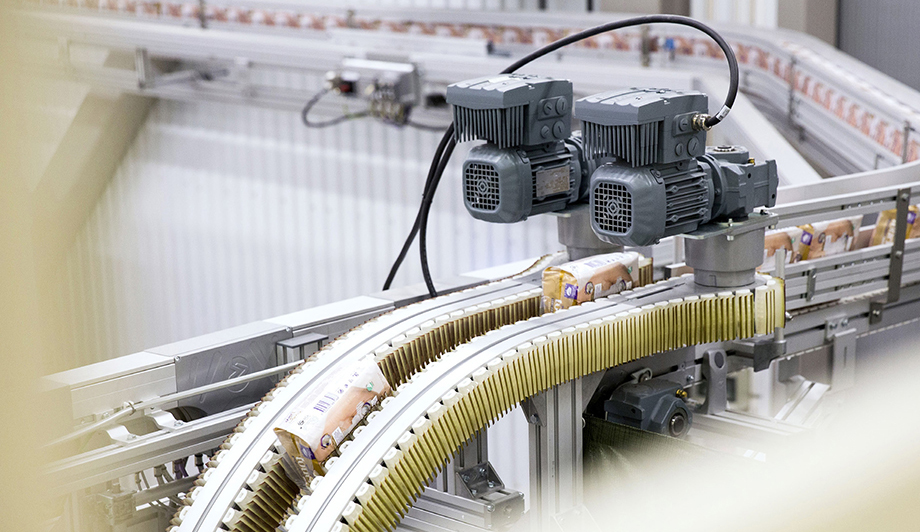
Essity is working to leverage global economies of scale and expertise to streamline all parts of the business and establish a world-class supply chain. Two global units are responsible for sourcing, production, logistics and technology: Global Hygiene Supply Personal Care and Global Hygiene Supply Tissue.
Safety first
Essity’s aim is zero workplace accidents. Sadly, a contractor was fatally injured during 2017 in a fire at our factory in Svetogorsk in Russia. The fatal accident emphasizes how important it is that safety efforts must always be prioritized and developed. Essity is working to nurture a culture where safety is top of mind and where unsafe working conditions and behaviors are immediately reported and rectified in order to prevent future accidents. Our employees continuously receive training so that everyone in the organization will be able to detect and eliminate hazards.
During 2017, the accident frequency rate decreased by 6% and in 2014–2017 it fell by 38%. The target is to reduce the accident frequency rate by 50% between 2014 and 2020.
Resource efficiency
To achieve the objective of contributing to a circular and sustainable society while increasing cost savings, Essity focused on reducing resource consumption during the year. Essity is operating two programs, ESAVE and MSAVE, designed to reduce energy and materials consumption. The aim of the programs is to achieve the best overall cost and minimize environmental impact. Our production facilities throughout the world share best practice and improvement measures to attain optimal results. The sourcing of raw materials is coordinated centrally in efforts to utilize economies of scale and during the year we increased savings when negotiating prices. In the Personal Care business area, a Flexibility Program was completed during the year aimed at qualifying new materials and suppliers more quickly, which contributed to further savings from sourcing.
During 2017, ESAVE projects were implemented that resulted in reductions in energy consumption by 0.4% per ton of product produced. Carbon emissions in relation to production level were reduced by 1.3%.
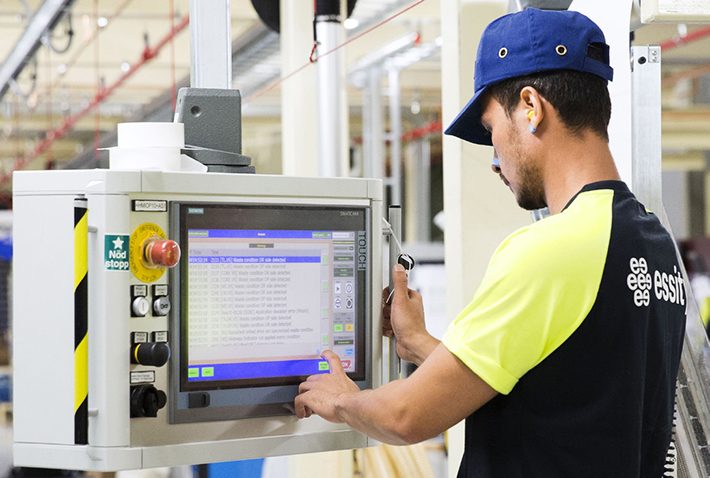
Digitalization for improved efficiency
Data analysis is used increasingly in production to increase product quality and reduce the risk of quality fluctuations. Using data analysis, we rapidly detect fluctuations and can establish the cause and thus take actions more quickly. This has led to higher product quality and also enables production to cope with a higher degree of complexity and a faster pace of innovation.
By equipping machines with QR codes, we have made it easier for our machine operators to quickly find relevant documentation about the machine, such as settings, technical drawings, work instructions and supplier data. The machine operators scan the QR code on the machine using a handset and gain direct access to relevant documentation, whereby, for example, production stops can be resolved more quickly.
ESAVE
Essity has received recognition for its efforts to combat climate change by means of improved use of energy. Essity recently won the ener.CON Europe Award 2017 for energy efficiency. Essity’s approach in the area was praised; for example, a company culture characterized by resource-efficient thinking, behavioral change, smart investments and an advanced IT system that shares information globally in real time.
Digitalization for world-class production
During the year, the work to optimize asset utilization at our production facilities continued, for example, by reducing the number of unplanned stops, increasing machine speed and investing in digital solutions. Through digital solutions, such as self-regulating machines, smart sensors, data analyses and robotic process automation, we increase product quality, production pace and flexibility.
Essity’s work on increasing machine efficiency enables more efficient utilization of existing production lines. The establishment of more efficient and flexible production facilitates speed to market in customer adaptations and innovations. Global Hygiene Supply cooperates closely with our innovation teams to develop the right technology and ensure access to optimal materials in order to safeguard speed and quality of our product launches.
Tissue Roadmap
To improve efficiency and increase value creation in the Consumer Tissue and Professional Hygiene business areas, Tissue Roadmap was launched in 2016. Through Tissue Roadmap, Essity is dedicated to achieving the lowest cost position combined with the best quality in each market in which we choose to compete. This is a roadmap to creating a world-class supply chain, improving cost and capital efficiency, securing capacity for future growth and enabling faster production adaptation in conjunction with innovations and product upgrades. The plan combines structural and organic efficiency opportunities in the supply chain with capacity expansion in selected markets.
To mitigate a tougher market with higher raw material costs, work under the Tissue Roadmap was intensified in 2017, resulting in increased cost savings.
During the year, Essity took actions to strengthen its tissue business in a number of markets. To meet growing demand for high-quality tissue and strengthen the product offering, Essity is investing in a through-air drying (TAD) machine in the UK. In addition, we closed an older tissue machine and divested a tissue production facility in the UK. To further strengthen competitiveness and enable future growth in Mexico, we decided to invest in one of the company’s tissue production facilities in the country. The investment will support Essity’s high-quality tissue offering under the Regio brand. In 2017, to further improve efficiency and strengthen the competitiveness of the Professional Hygiene business in North America, Essity closed a tissue production facility in the US.