Drive efficiency
Essity is working to leverage global economies of scale and expertise to continuously increase efficiency in all parts of the business, from the supply chain to sales and administration. We are working to establish a world-class supply chain. By improving productivity, reducing material, energy and logistics costs and minimizing waste, we reduce our costs and improve our earnings at the same time as we reduce the environmental impact.
Safety first
Essity is working to nurture a culture where safety is top of mind and unsafe working conditions and behaviors are immediately reported and rectified in order to prevent accidents. Essity’s aim is zero workplace accidents. Our employees continuously receive training so that everyone in the organization will be able to detect and eliminate hazards. In 2018, the theme of Essity’s annual global safety week was “Everyone is a safety leader — so are you.” During 2018, the accident frequency rate decreased by 1% and in 2014–2018 it fell by 39%. The target is to reduce the accident frequency rate by 50% between 2014 and 2020.
Digitalization for world-class production
During the year, we continued to implement digital solutions including self-regulating processes, smart sensors, data analyses and robotization and automation to improve product quality and efficiency.
Cost savings
We have intensified our efficiency improvements and restructuring of the business and achieved SEK 1,040m in cost savings during the year.
To improve efficiency and increase value creation in the Consumer Tissue and Professional Hygiene business areas, Tissue Roadmap was launched in 2016. The aim is to achieve the lowest cost position combined with the best quality in each market in which we choose to operate. As part of the Tissue Roadmap, we took decisions during the year on restructuring measures in Europe, North America and Latin America.
To improve profitability and strengthen long-term cost efficiency, Essity introduced a Group-wide cost-savings program in September 2018. The program is expected to generate annual cost savings of approximately SEK 900m, with full effect at the end of 2019. The cost-savings program is being implemented in all parts of the Group to reduce the cost base related to cost of goods sold and costs for sales, general and administration. The program includes headcount reductions of approximately 1,000 positions and is in addition to the efficiency initiatives already in progress in the company, for example Tissue Roadmap.
Reduced resource consumption
To achieve increased cost savings while contributing to a sustainable and circular society, Essity continued its work during the year on reducing material and energy use. The accumulated energy savings in the 2010–2018 period amounted to 8%.
New organization for increased efficiency
Changes were implemented to the company’s organizational structure and Executive Management Team in 2018. For example, the two units Global Hygiene Supply Tissue and Global Hygiene Supply Personal Care were merged into one unit, Global Manufacturing, with responsibility for production and technology. A new unit, Global Operational Services, was created in order to further strengthen the Group’s overall work related to operational and cost efficiency. The unit encompasses sourcing, logistics, business services, IT and digitalization. The number of Group functions was reduced from six to four.
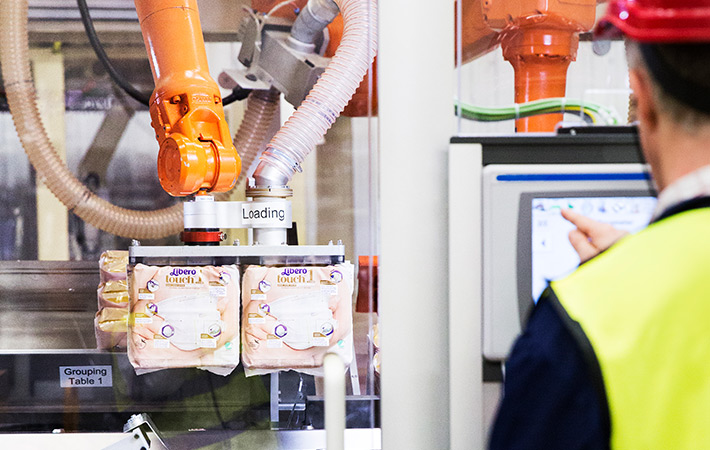
Digital quality controls
In 2018, our Personal Care facility in Hoogezand, the Netherlands, has worked to replace the manual quality control of production lines with digital controls to improve both product quality and efficiency.